What Is A Downfall To Just-In-Time Manufacturing And Inventory Management?
- mark599704
- Feb 23, 2024
- 7 min read
Updated: 3 days ago
Just-in-time (JIT) manufacturing and inventory management is a method that has been praised for improving production processes. It helps in cutting costs by making everything more efficient. The concept revolves around producing goods and acquiring inventory only when they are needed, thereby minimizing excess inventory and associated costs. However, despite its numerous advantages, there are several potential downfalls to implementing JIT manufacturing and inventory management systems. We will look at the downsides in this article. We will also discuss the challenges businesses might face when using this approach.
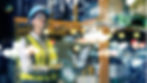
Related Blogs:
What is Manufacturing Inventory Management?
First, you need to learn the basics of inventory management in the manufacturing industry. Then, you can look into the possible problems with JIT manufacturing and inventory management. Inventory management is about keeping track of raw materials, work-in-progress, and finished goods. It helps control how these items move through a manufacturing facility. It involves strategically balancing the levels of inventory to ensure smooth production processes while minimizing inventory holding costs.
What is a Downfall to Just-in-Time Manufacturing?
Just-in-time manufacturing has several potential pitfalls that businesses must be aware of. One of the main challenges is the increased vulnerability to supply chain disruptions. Since JIT needs a perfectly timed supply chain, any problems with getting raw materials or parts can greatly affect production schedules. This can lead to delays in meeting customer demand and potential loss of business.
Another downfall of JIT manufacturing is the limited adaptability to sudden changes in customer demand. JIT systems are designed to respond swiftly to customer orders with minimal lead times. However, if customer demand fluctuates unexpectedly, it can be challenging to adjust production levels accordingly. This might lead to having too much inventory or running out of stock. Both situations can have big financial effects on the business.
Retail vs. Wholesale Inventory Management
When it comes to inventory management, there are distinct differences between the retail and wholesale sectors. Retail inventory management focuses on meeting the immediate needs of customers, with a greater emphasis on just-in-time inventory management. Wholesale inventory management usually deals with bigger quantities. It also takes more time because of how the business works. Wholesalers often need to maintain higher inventory levels to cater to diverse customer demands, making JIT implementation more challenging.
Just-In-Time Manufacturing and Inventory Management
Just-in-time manufacturing and inventory management are closely intertwined. JIT manufacturing aims to eliminate waste and improve efficiency by producing goods only when they are needed. This requires a well-coordinated production process, with precise timing and synchronization of activities. Meanwhile, JIT inventory management focuses on minimizing inventory levels to reduce costs associated with holding excess inventory.
Why Inventory Management is Critical for Small Manufacturers
Inventory management plays a crucial role in the success of small manufacturers. Here are some reasons why it is critical for their operations:
Cost Savings
Effective inventory management allows small manufacturers to optimize their inventory levels and reduce holding costs. By avoiding excess inventory, businesses can minimize storage expenses, obsolescence, and the risk of stockouts. This leads to significant cost savings in the long run.
Increased Efficiency
By implementing JIT manufacturing and inventory management principles, small manufacturers can streamline their production processes and eliminate bottlenecks. This leads to increased efficiency and reduced lead times, enabling businesses to respond quickly to customer demands.
Improved Customer Satisfaction
Efficient inventory management ensures that small manufacturers can meet customer demands promptly and consistently. This leads to improved customer satisfaction and loyalty, which are essential for long-term business success.
Scalability
Effective inventory management practices lay the foundation for scalability. Small manufacturers can expand their operations smoothly by optimizing inventory levels. They can also use JIT principles to avoid high inventory costs.
Common Manufacturing Inventory Metrics
To measure the effectiveness of inventory management, several metrics are commonly used in the manufacturing industry. Some of the key metrics include:
Turnover Ratio:Â Measures the number of times inventory is sold or used within a specific period.
Cost of Goods Sold (COGS):Â Calculates the direct costs associated with producing goods.
Economic order Quantity (EOQ):Â Determines the optimal order quantity to minimize inventory holding and ordering costs.
Days Inventory Outstanding (DIO): Provides insights into the average number of days it takes for inventory to be sold or used.
Reorder Point: Represents the inventory level at which a new order should be placed to avoid stockouts.
Safety Stock: Additional inventory held as a buffer to mitigate uncertainties in demand or supply.
Minimum Order Quantity: The smallest quantity that can be ordered to ensure cost-effective procurement.
Maximum Inventory Level:Â The upper limit of inventory that a business can hold to avoid excessive costs.
Dependence on Precise Coordination and External Partners
JIT manufacturing and inventory management need careful coordination with external partners. This includes working closely with suppliers and logistics providers. However, this dependence on external partners can pose several challenges:
Challenges in Dealing with Unforeseen Circumstances or Changes in Demand Patterns
Even with careful planning, unexpected events can still affect the supply chain. This can delay the delivery of raw materials or components. This requires businesses to have contingency plans in place to mitigate any potential disruptions.
Increased Vulnerability to Price Shocks and Limited Adaptability
JIT manufacturers rely on a steady supply of raw materials and components at stable prices. However, sudden price increases can significantly impact the production costs, potentially affecting profitability. Moreover, JIT systems may struggle to adapt quickly to sudden changes in production requirements or customer demand.
Manufacturing and Inventory Management Terms
To understand JIT manufacturing and inventory management, you need to know some key terms. These terms are important for grasping the main ideas:
Just-in-time Inventory Management:Â A production strategy that aims to minimize inventory levels by producing goods only when customer demand exists.
Continuous Improvement: The ongoing effort to improve processes, products, and services to enhance efficiency and quality.
Quality Control: The process of ensuring that products meet predetermined quality standards through inspections and testing.
Just-in-time Inventory System:Â An approach that focuses on maintaining minimal inventory levels and relies on precise timing and coordination.
Excess Inventory:Â Inventory levels that exceed current customer demand and tie up valuable resources.
JIT Manufacturers:Â Businesses that have adopted the just-in-time manufacturing philosophy and implement JIT principles in their production processes.
Significant Investment in Information Technology Infrastructure
Implementing JIT manufacturing and inventory management systems often requires a significant investment in information technology (IT) infrastructure. Here are some key considerations regarding IT infrastructure and its importance for successful JIT implementation:
The Importance of IT Infrastructure for JIT Implementation
IT infrastructure is very important for smooth communication. It helps different departments and partners in the supply chain work well together. It facilitates real-time data sharing, order processing, and inventory tracking, allowing for better decision-making and synchronization.
Challenges Faced by Smaller Enterprises with Limited Budgets
Smaller enterprises may struggle to make the necessary investments in IT infrastructure due to budget constraints. There are budget-friendly solutions available. Cloud-based systems and software-as-a-service (SaaS) options can help small businesses handle these problems.
Inventory Management Formulas
To manage inventory levels well, businesses use different formulas. These formulas help them calculate important numbers and make smart decisions. Here are some commonly used inventory management formulas:
Turnover formula
Inventory turnover = Cost of goods sold / Average inventory value
Cost of goods sold formula
Cost of goods sold = Opening inventory + Purchases - Closing inventory
Economic order quantity (EOQ) formula
EOQ = √[(2 × Annual usage in units × Ordering cost per order) / Holding cost per unit]
Days inventory outstanding (DIO) formula
DIO = (Average inventory value / Cost of goods sold) × 365
Reorder point formula
Reorder point = Lead time demand + Safety stock
Safety stock formula
Safety stock = Z-score × Standard deviation of demand during lead time
Minimum order quantity formula
Minimum order quantity = Economic order quantity × (1 - (Discount rate / 100))
Maximum inventory level formula
Maximum inventory level = Reorder point + Economic order quantity - (Demand during lead time × Unit cost)
Conclusion
Just-in-time manufacturing and inventory management have many benefits. However, it's important to recognize the possible downsides of this approach. Businesses need to think carefully about the problems caused by supply chain disruptions. They also need to manage their ability to adapt and coordinate precisely with external partners. Small manufacturers need to focus on managing their inventory well. This helps them save money, work more efficiently, make customers happier, and grow their business. Understanding common inventory metrics, terms, and formulas helps businesses. This knowledge makes it easier to handle the challenges of JIT manufacturing and inventory management.
Frequently Asked Questions (FAQs)
1. What is Just-In-Time (JIT) manufacturing and inventory management?
Just-In-Time (JIT) refers to producing goods or acquiring inventory exactly when needed—no sooner, no later. This approach reduces excess inventory and associated costs, aiming for lean efficiency in production systems.
2. What are the main downfalls or risks associated with JIT?
The article highlights several critical drawbacks:
Vulnerability to supply chain disruptions:Â Any delays or issues in obtaining raw materials can severely impact production schedules and lead to customer dissatisfaction.
Limited adaptability to sudden customer demand changes: JIT systems may struggle when demand fluctuates unexpectedly, leading to stockouts or surplus inventory—both of which can be financially damaging.
3. Why might retail and wholesale sectors experience different outcomes with JIT?
Retail businesses prioritize meeting immediate customer needs, making JIT more applicable for them.
Wholesale operations often handle large volumes and longer lead times, making JIT implementation more challenging due to their need for consistent stock levels.
4. Why is robust inventory management crucial for small manufacturers?
For small manufacturers, effective inventory management helps:
Save on costs by reducing storage, obsolescence, and stockout risks.
Increase efficiency and streamline production workflows.
Enhance customer satisfaction by meeting demand reliably.
Support scalability in operations by optimizing inventory levels and adopting lean processes.
5. What key strategies or terms should readers understand to better grasp JIT and inventory management?
Understanding these terms and concepts is essential:
Just-In-Time Inventory Management:Â Delivering or producing items only as customer demand arises.
Continuous Improvement: Ongoing efforts to enhance processes and reduce inefficiencies.
Quality Control: Ensuring products meet standards via testing and inspection.
Excess Inventory:Â Inventory that exceeds demand levels, tying up resources.
JIT Manufacturers: Businesses that operate using JIT philosophy and methods.